How about some plastic?
Tips from the blowmold queen

Known by various names including Light-ups, Lawn Art, kitsch, illuminated figures, or simply blow molds (two words, not one), they are a type of Christmas decoration that become an obsession for many. Who are the “blow molders” and what are they after? They’re another segment of the Christmas decorating community with a passion for the good old days and a desire to bring the joy of the season to everyone.
Blow molds are not just milk jugs, soda bottles, and gas tanks. To a blow mold enthusiast they are Santa in his sleigh, elves carrying gifts, prancing reindeer, a battalion of snowmen, candles, wreaths, candy canes, lanterns… three dimensional, durable, colorful and bright.
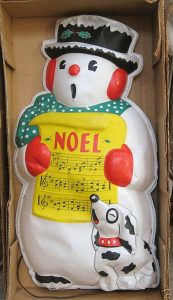
Blow molding is a plastic manufacturing process. In 1881, the first U.S. Patent was given to Celluloid Novelty Co. of New York for extruding a polymer (called cellulose nitrate) into a parison. In a nutshell, a hollow tube (the parison) is filled with melted plastic, placed into a steel mold and inflated with air or gas which forces the plastic to the interior surface of a metal mold. Upon cooling, the metal mold is opened and the item is removed and appropriately painted. Cellulose acetate was later used in the 1930’s followed by Low Density Polyethylene (LDP) in the 1940s causing the blow molding industry to quickly grow when Monsanto started making plastic squeeze bottles. Ever see those plastic ketchup bottles at the local diner? They were the forerunner to Santa.
Soon many other manufacturers started using the process to produce plastic containers in substitution for glass. In the 1950’s High Density Polyethylene (HDPE) and Polypropylene (PP) were used to produce containers for water, oil, and most importantly, the lowly milk jug; revolutionizing the dairy industry. In future articles you’ll understand why the milk jug has become important to today’s blow mold community. Without it, blowmold repairs would be much more challenging.
OK. Enough of the scientific sounding jargon.
It’s important to mention that prior to the advent of blow molded Christmas decorations, various manufacturers such as Raylite, Artform, Royalite, Glolite and NOMA had been successfully selling plastic decorations, candy containers, knick knacks and Christmas plaques. These plaques, affectionately referred to as “flat backs” were made of various plastic formulations using the vacuforming manufacturing process. A sheet of plastic would be heated and placed on a one sided steel or aluminum mold. A vacuum would be applied between the mold and the sheet of plastic creating a raised, two dimensional design. These shallow plastic plaques were cheerful, colorfully painted, available in a plethora of designs and in many cases internally lit by one or more C7 bulbs. The back of the plaques were made of various materials ranging from tin to cardboard that was stapled, screwed or glued to the plastic fronts and equipped with a convenient cutout or hook for hanging on a wall. These plaques were very popular but fragile.
Early in the 1960s, enterprising manufacturers started producing blow molded Christmas decorations. Beco Products Corporation of Chicago made a large splash in the Christmas decoration world by producing and catalog marketing a fully three dimensional Santa, sleigh and reindeer set. In the initial release (believed to have been in 1963 -1964) the Santa came equipped with a unique bottom mounted light kit, but sadly his white reindeer were not made to light. Beco soon realized the error of its way and thereafter produced its deer blow molds with a light kit. Beco created many winning designs including a mechanical Santa that has been aptly described as “bowing” from the waist. Unfortunately, the company’s life span was short lived. The exact year that Beco ceased its operations is unconfirmed, but is believed to have been in the late 1960s to as late as 1972.
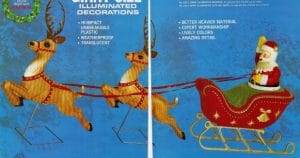
Not to be outdone, Poloron Products of New Rochelle, NY got involved. The company widely known for its picnic coolers and thermos jugs (still available on eBay) produced a beautiful selection of blow molded decorations and marketed their Christmas products primarily through the Sears catalog. Poloron’s products (forgive the pun) were very highly detailed, skillfully painted, and extremely durable blow molds. Poloron’s addition of mechanicals and motors to a Santa and a snowman, causing each of them to swivel at the waist gave a new dimension to the lowly plastic light up.
It didn’t take long before the American Christmas landscape was dotted with plastic Santas, reindeer, elves, snowmen, carolers and choir people. Blow molds were anywhere from just over a foot tall to nearly life size.
Over the years, many manufacturers produced hundreds of designs and variations on their own paint schemes. Some of the more well known companies were (in alphabetical order): Bayshore, Beco, Borce, Borse, Carolina Enterprises/Empire, Dapol, Drainage Industries, Farley, General Foam Plastics, Grand Venture, Hamilton Skotch, Holiday Innovations, Lidco, NOMA, Nu-Dell, Poloron, Santa’s Best, Sunhill, TPI and Union Products.
As the companies have come and gone many of the steel molds were sold from one manufacturer to the next. For example, when Poloron ceased doing business in the 1970s some of their steel molds were sold to Holiday Innovations which produced their own version of the design. The vast selection, including all the varietals of a single mold, creates a never ending quest for the collector/displayer/enthusiast.
Whether you call them blow molds, light-ups or kitsch, the durability, beauty and delighted smiles of young and old alike have given blow molds a unique and beloved place in the Christmas decorating pantheon. Don’t worry. There’s more to come.
This article was included in the November 2009 issue of PlanetChristmas Magazine.
By Carrie Polales Sansing